Automating industrial processes and digitizing records to improve effecency
Outcome
Automate the operation and recording of mobile equipment, so users are able to quickly and accurately manage resource and waste levels at remote locations and eliminate tedious, unreliable, hand written records.
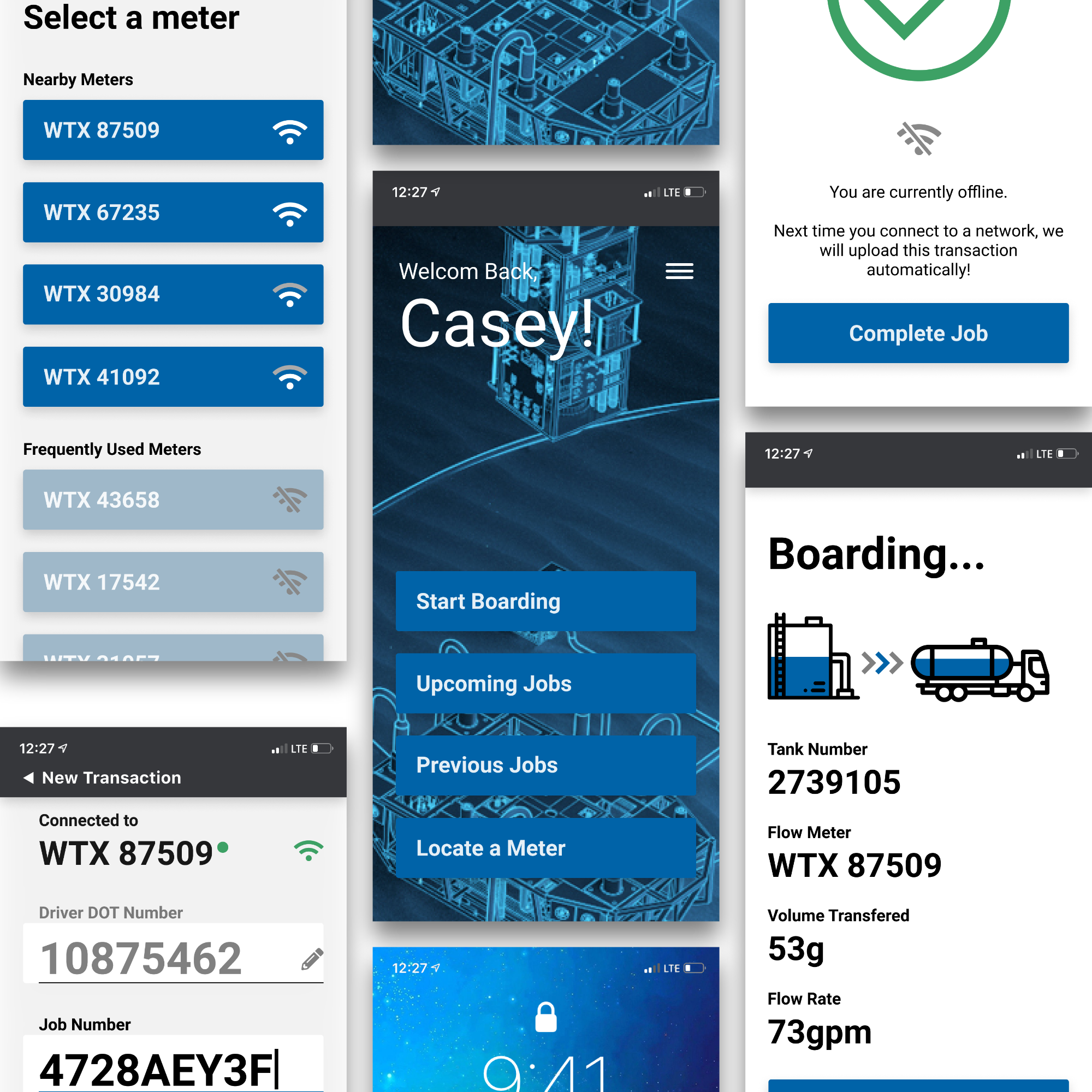
Designed for Use
Through research and observation of the processes in their current state, I established 3 user-centric design principles for this project:
- Ease of use within environmental constraints
- Simplify the existing process
- Create clarity for users
Ease of use within environmental constraints
Operators must to drive to remote locations to collect waste material and manage several pieces of equipment at each stop. These sites are isolated and often lack any form of internet or cellular connection. The waste removal process occurs outdoors, regardless of weather and other environmental conditions. Additionally, the operators are required to wear Personal Protection Equipment (PPE) such as safety glasses and cut-resistant gloves.
These constrains lead to many design decisions, such as:
- Large, easy to read text for clarity in bright environments
- Large buttons and tap targets for easier interaction while wearing gloves
- Visual process indicators to help operators understand what was happening inside the equipment
- Display the critical information only to avoid confusion and promote accurate record keeping
- Graceful handling of loss of connectivity to minimize interruption to users while in remote areas
Simplify the existing process
The process for operating the equipment and collecting waste material at each site was manual and prone to mistakes such as:
- Handwritten records that were often inaccurate or incomplete
- Manual operation of equipment prone to damage or loss of valuable materials
- Manual data entry that was time consuming, error prone, thus unlikely to be done at all
To combat this, the application was paried with new, low cost, connected control systems, allowing the complexity of the equipment operation to be automated and standardized. This ensure the equipment was left operable and without damage after the waste removal process was complete
Additionally, focus was placed on creating records automatically, storing them when offline and automating data synchronization.
Create clarity for the user
Operators were required to manage multiple pieces of equipment at each site, each with its own set of controls and processes. The application was designed to make it obvious to the user which piece of equipment they were meant to me operating according to the current work order, and which piece of equipment they were currently connected to in the application.
Additionally, the application was designed to provide feedback and control over the equipment and process to protect the equipment and save the user time by reducing manual checks on progress.
Prototype
Below is a prototype of the application that was used to test the design with users and stakeholders. This prototype represents one of the flows a user would take to complete the waste material removal process.